Assembly and Connection Technology for E-mobility Solutions and Power Electronics
For bonding semiconductors such as IGBTs, SiC MOSFETs or GaN HEMTs with Ag on DBC or AMB substrates or for connecting power modules on heat sinks, metallic sintering offers a high-performance assembly and connection technology with maximum reliability. Tresky’s sinter bonders enable the use of copper sinter paste, thixotropic silver paste, and DIE Transfer Film (DTF).
Metallic Sintering
When performing sintering, the chip is bonded to a substrate using sintering paste with the aid of heat and pressure. Typically, copper or silver sintering pastes are used. During the actual sintering process, the metal particles are bonded together by diffusion processes. The advantage over soldering processes is better thermal conductivity, longer service life and high thermomechanical stability. These properties are particularly important in electromobility and power electronics.
Precise application of the paste is the first step for a reliable, reproducible pre-sintering process in assembly and connection technology. For this purpose, Tresky uses the SQ-Nozzle developed for this purpose, which ensures a very homogeneous and large-area application of paste. The repeatability of the defined layer height or thickness is validated by an optical measurement system. After application of the sintering paste, the power semiconductor is placed within the machine in a second process step.
Flyer Sinter Bonder PDF (EN)
White Paper: Motivation for Sintering in Semiconductor PDF (EN)
White Paper: Large Area Sintering (Half-Bridge Modules) in Power Electronics PDF
Benefit from 20 years of experience in electronics, semiconductor and battery production
Your bonding process
For bonding semiconductors, such as IGBTs or SiC MOSFETs with Ag or Au on DBC or AMB substrates or for connecting power modules on heat sinks, metallic silver or copper sintering offers a high-performance solution with maximum reliability. If you are considering sintering as a bonding process, we offer you comprehensive solutions, from consulting, feasibility studies and process implementation to extensive after-sales support.
Consulting
Our process consulting and training services help you to holistically evaluate manufacturing by means of metallic sintering and to derive the process selection and parameters for the production of your end products. Take advantage of our 20 years of experience in the fields of electronics, semiconductor and battery production. We actively support you in the development up to the series production of your products.
Process development
We have developed a number of pre-processes for sintering that contribute to cost and effort reduction of the overall process. These include hot mounting or tacking of semiconductors, but also dispensing of sintering paste and force-controlled placement of semiconductors or modules on heat sinks. These processes can be adapted to production specifications and product configurations. If this is not sufficient, we develop individual processes, as we have been doing for the semiconductor industry for years.
Evaluation
If sintering is your favoured assembly and connection technology, for example in a power module project for e-mobility, we will be happy to support you in the selection of the individual steps, according to your end product, the production volume and the specified cost framework. Based on this evaluation or assessment, we can make suggestions about changes, structure and process optimization and thereby reduce the time-to-market.
Feasibility study
We carry out feasibility studies for you in our application laboratory. We check the overall solution approach with regard to technical feasibility and application. Depending on whether you want to use metallic sintering for bonding semiconductors to circuit carriers or circuit carriers are to be sintered to base plates, there are different process requirements.
Project management
Once the evaluations and feasibility studies have delivered a clear picture of the structure of the production process around sintering, we support you in the project management and planning of this assembly and connection process. In doing so, we rely on our broad network and, after agreement with you, bring other partners into the team, e.g. for vacuum brazing or analysis.
Pre-Sintering Processes on Sinter Bonders from Tresky
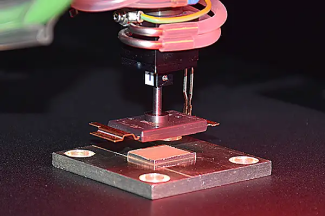
Prototype and batch size 1 production
In the prototyping phase, in the production of small series or batch size 1, many companies hesitate to invest in their own production line. We will gladly take over this service for you and, with a great deal of technical know-how and our many years of experience, manufacture the prototypes and small batches for you from the first piece on our systems.
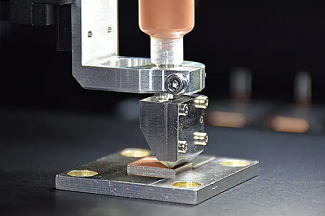
Sintering paste application
In order to optimize the entire process of sintering with regard to costs and cycle times, we have developed and implemented our own process technologies. By using a dispenser SQ-Nozzle, large-area deposits of silver or copper sintering paste can be applied sequentially and very precisely. The sintering paste can thus be dispensed onto the substrate in a defined layer height and width in one process step. For process control, the layer thickness of the applied paste depot can be measured directly by laser.
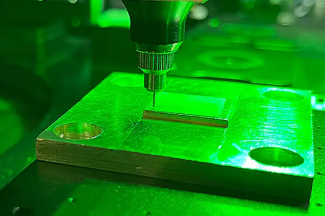
Dispensing of tacking agent
The hot pick and place process is a common method of placing semiconductors for sintering. However, oxides can appear on the bare copper surface of the chip when the substrate is heated. This oxidation can be avoided by conducting the placement at room temperature. In this case, it is necessary to fix the component on the sintering paste to ensure accurate positioning on the transport route to the next process. Therefore, the chips are usually provided with an alcohol-based tacking agent.
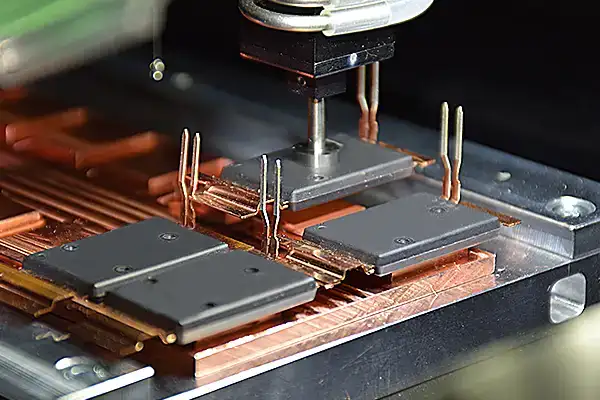
Pick & place of components
An important process is the picking and placing of semiconductors. When using sintered matrices, hot tacking is used. This avoids any movement during transport into the sintering press. This process, also called hot pick and place, differs from the standard sintering process with pre-dried and thus no longer sticky sintering paste.
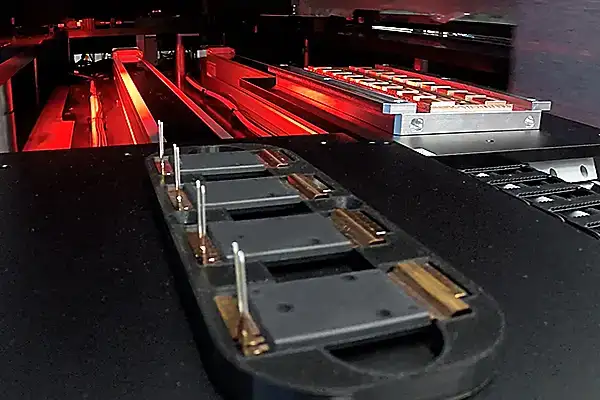
Inline or batch mode production
All DIE bonders from our machine portfolio can be used as sintering bonders. It is possible to work in both inline and batch mode. In inline mode, the DIEs and substrates are automatically transported into the machine and produced in an uninterrupted process. In batch mode, the machine is loaded manually by an operator with DIEs and substrates, e.g. in trays as waffle packs. All the production steps required for the pre-sintering process (tacking) then take place within the machine.