- Home
- Products
- Sintering Bonder
- Large Area Sintern
Large Area Sintern
Large Area Sintering (Half-Bridge Modules) in Power Electronics
The integration of large-area power modules and half-bridge modules with an area of over 100 mm² is highly relevant. These modules are of great importance for various applications in e-mobility, as they offer high power density and efficiency.
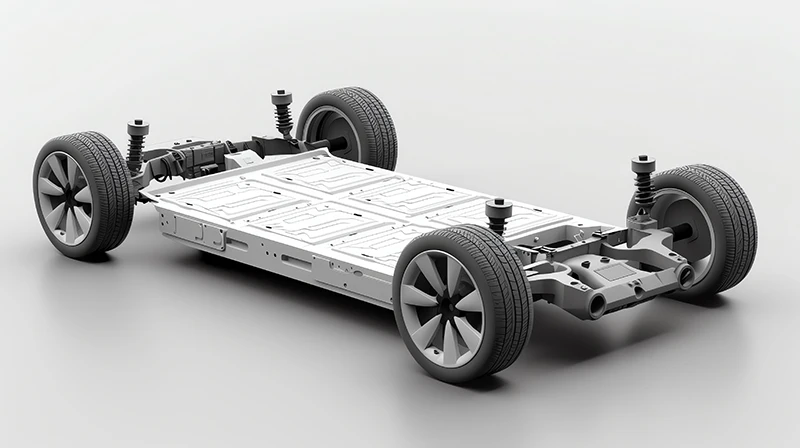
Tresky allows dispensing of over 100 mm² for large area sintering applications
However, connecting these components is challenging. Bonding of components, AMB substrates, or PCBs used with heat sinks using silver sintering become a high technical challenge. Factors such as warpage, surface quality, and the application and processing of pastes become increasingly complex. In particular, problems arise during the dry sintering process for large power semiconductor modules, such as the difficult printability of large areas with the paste printer, the formation of depressions, also known as cavities, and warping on the AMB substrates or modules themselves. Air pockets (voids) can form between the substrate and power module, affecting the connection and potentially leading to microcracks.
Reproducible wet sintering process
The wet sintering process offers a promising alternative. In this process, the wet sinter paste is applied to the substrate on a large area using a dispensing method, and the module or semiconductor is then placed directly into the paste. This method allows for compensating for the warpage of components such as the substrate and semiconductor chip through the wet sinter paste. Minimal layer thicknesses can be achieved through the dispensing process. Large Area Sintering can reduce material consumption and production costs.
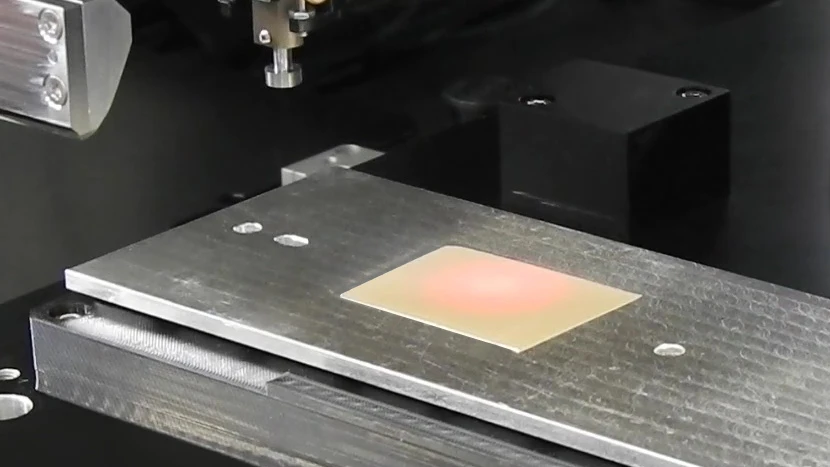
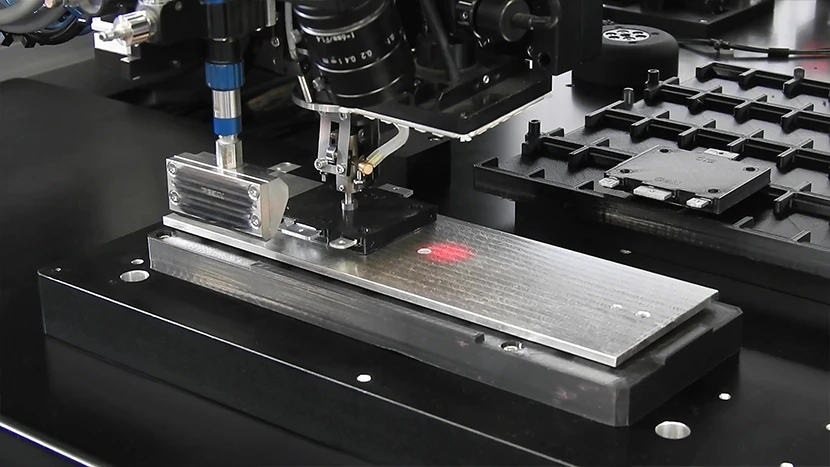
Development and optimization of sintering processes
The development and optimization of these specific sintering processes are crucial for producing reliable and efficient large-area power semiconductor modules. Improving connection techniques and reducing defects also increases the modules’ lifespan, leading to higher performance and operational safety, for example, in electric vehicles.
Continuous research and innovation in this area are essential to meet the industry’s increasing demands and drive technological development forward. Advanced sintering processes significantly contribute to competitiveness and sustainability, especially in e-mobility and power electronics, where efficiency and reliability are of central importance.